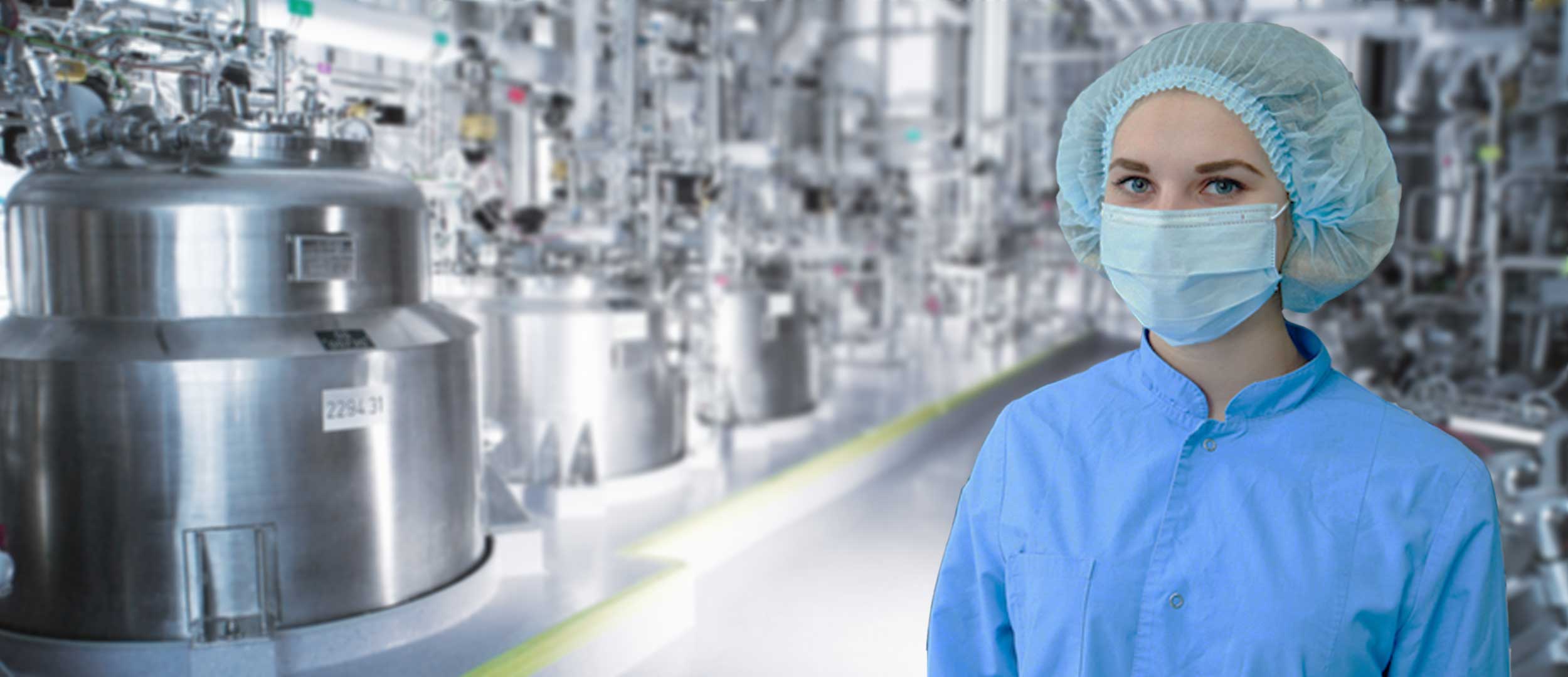
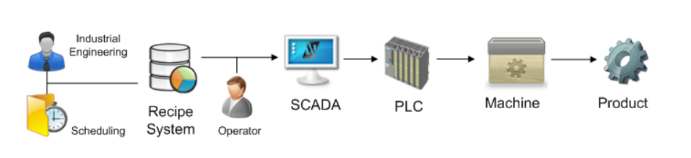
If you’ve read my blog’s from the last several months, you’ll notice I am really pushing the fact that data not stored electronically is ‘dead data’.
I have spent most of my professional career collaborating, designing, and implementing Software Mediated production systems. Using a blend of hardware and software to help companies realize productivity gains has been my work’s mission.
Along the way, the one benefit of Software Mediated Systems, is the ability to capture real-time data - information happening at a given moment in time - into databases and plant wide historians. Collecting data from shop floor control systems with Kepware, Matrikon, and OAS have been tools we have all been using for over twenty years to populate the data historians like OSI PI and Aspentech.

This has been a great benefit for both the companies implementing the systems and the employees using the system. Having the ability to replay the history of what took place in a given production run is of incredible value to an organization. If you know or heard of anything associated to Machine Learning and Predictive Analysis, it is this data that the Data Scientists want to get their hands on in order to help companies make better decisions about future production runs (i.e. mitigate production problems early in the production run to shorten cycle times and improve yields).
A well designed system also augments the employee on the shop floor and allows him or her to be more effective, faster, and safer in the given production environment. The employee is bigger and better with the the system.
Manufacturing Execution Systems
The system presented is essentially a Manufacturing Execution System (MES). This system delivers a ‘recipe’ or instruction set of how to take inputs (i.e Raw Materials, intermediates, and human labor) and produce outputs ( final products and intermediates). The MES systems orchestrating and using the lower level hardware and software (DCS and PLC Systems) are evidence of the some of the greatest advancements in productivity over the last two decades.
I think we are now at a point that as thought leaders and managers within our industries, we should think about the following: ‘(fill in the blank) Execution Systems’. That’s right. If it works so well for the manufacturing and the operations portion of our companies, we should look at and ask ourselves what other information and processes are important to our companies ‘outside’ of what is usually collected inside of a ‘batch’ or production run. Are other activities within my organization important to the operational efficiency of the company I work for?
The most basic concept of something being efficient for a company is a defined repeatable process. If we can put a recipe to a given process, we can automate it, store the data, and realize productivity and cost savings. Wow…..let’s make everything an ‘Execution System’ or ES if you will…...Having a system in place that keeps all personnel within the ‘boundaries’ of what are acceptable limits and tolerances to perform any process is the key to less mistakes, less deviations, and less review and reconciliation of exceptions within a given work day.
For the purposes of this blog, let’s look at the one area that every company deals with every day.
Paper Logbooks - where data goes to die…....
Companies are swimming in the recording of data related to non-production information. Walk into any company today, big and and small, and paper log books are everywhere for everything.
Equipment, Calibration, Maintenance, and Cleaning logs are just a sample of the type of logbooks most companies keep. And much of it is kept in weekly and monthly paper look books that need to be reviewed by supervisors and managers. Just reading the sentence above, the image that comes to mind is lots of humans recording lots of data manually and lots of humans reviewing. Not to mention all the prep work every week and month to produce the blank log books that will be issued into an area.
Once recorded, the data is good for that ‘moment in time’ and then the paper logbooks are sent to both long and short term storage facilities. Once that review is done by a manager, the chance of realizing any real information from that data is gone. The ability to see maintenance trends or equipment trends is lost.
Digital Transformation
The answer is Digital Transformation. Moving the business processes forward is where the productivity comes from. Using field installed PCs, portable tablets, phones, and scanners (i.e. Zebra TC70) augment your workforce to be better today and tomorrow than they were yesterday. The new workforce expects this type of workplace augmentation. Intuitive software with the ease and use of a typical phone application is the key to success.
Software that operates effectively and intuitively is software that team members and employees want to use. That is a key statement. Acceptance of a system because it helps and doesn't hinder or hurt. And if everyone wants to use it, the time needed to transition between the old way of doing business and the new way of doing business is shortened and we all get to experience the benefits quicker.
If you think your company can improve in these areas, reach out to me via our website at https://www.deadlinesolutions.com and we can can have further discussions.
In my next blog, I will explore how Amazon’s AWS IoT and Microsoft’s Azure IoT can be used to further enhance these plant installed Software Mediation Systems.
Remember…...start small…..finish big!